A Brief Discussion on the Roots Blower Sealing Forms and Applications of Roots Blowers
The sealing of Roots blowers includes the sealing of the drive shaft extension, the tail oil seal of the bearing seat, and the shaft seal of the wall plate. The primary purpose of the wall plate shaft seal is to prevent gas leakage. The other two areas primarily prevent oil leakage, though they may sometimes also require gas sealing. Let’s have a look the Roots Blowers Sealing Forms today.
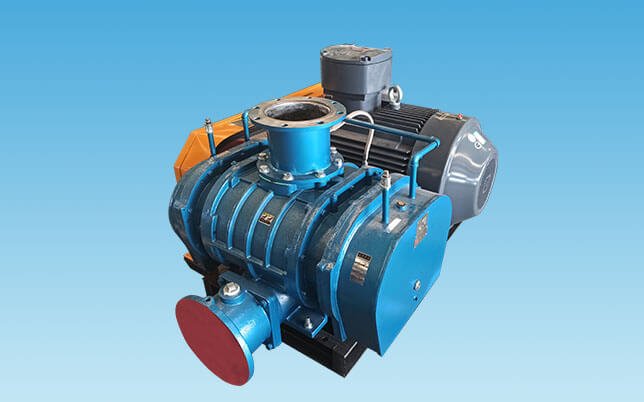
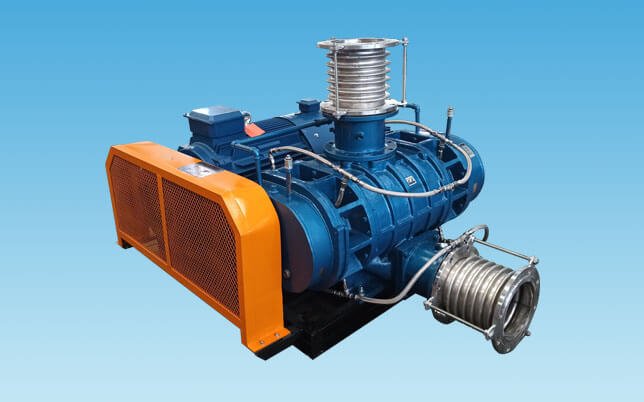
1. Gas Sealing Device
Structures that primarily seal gas are typically referred to as gas sealing devices, while those solely for oil sealing are referred to as oil sealing devices. Common sealing devices for the wall plate shaft seal in Roots blowers include labyrinth seals, packing seals, expansion ring seals, and mechanical seals. For the drive shaft extension, common sealing devices include skeleton oil seal groups or mechanical seals. The tail oil seal of the bearing seat often uses a return oil groove structure or skeleton oil seal groups.
1.1 Labyrinth Seal
The labyrinth seal is a non-contact dynamic seal that uses a passage composed of a series of throttling gaps and expansion cavities. It restricts leakage by inducing a throttling effect on the working medium. Labyrinth seals are widely used in the wall plate shaft seal of Roots blowers.
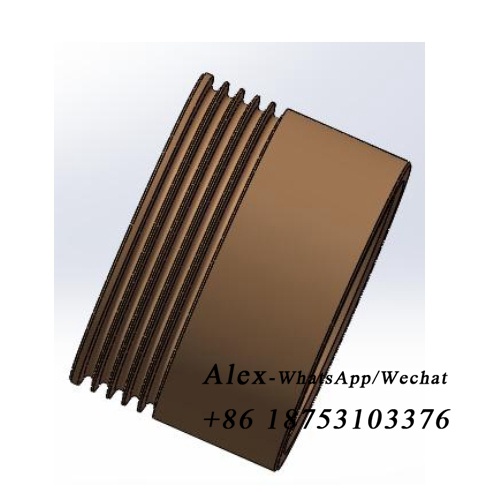
The labyrinth seal is a non-contact dynamic seal that uses a passage composed of a series of throttling gaps and expansion cavities. It restricts leakage by inducing a throttling effect on the working medium. Labyrinth seals are widely used in the wall plate shaft seal of Roots blowers.
Mechanism: The fluid passes through multiple winding passages, experiencing repeated throttling, which creates significant resistance and makes it difficult for the fluid to leak, thus achieving sealing.
Advantages:
- Unaffected by rotational speed and temperature.
- Simple structure, easy maintenance, and long service life.
- Effective for high-pressure gas sealing by increasing the number of sealing teeth.
Disadvantages:
- High precision requirements for sealing components.
- Small sealing gaps can lead to friction and wear during machine malfunction, reducing sealing performance.
Labyrinth seals are generally used in applications involving air transport but are limited in cases involving toxic, flammable, or explosive gases. Standard Roots blowers commonly use this sealing type for the wall plate shaft seal.
1.2 Packing Seal
The packing seal prevents leakage by filling the leakage passage with packing material. It is simple in structure, easy to assemble and disassemble, and cost-effective, making it widely applicable.
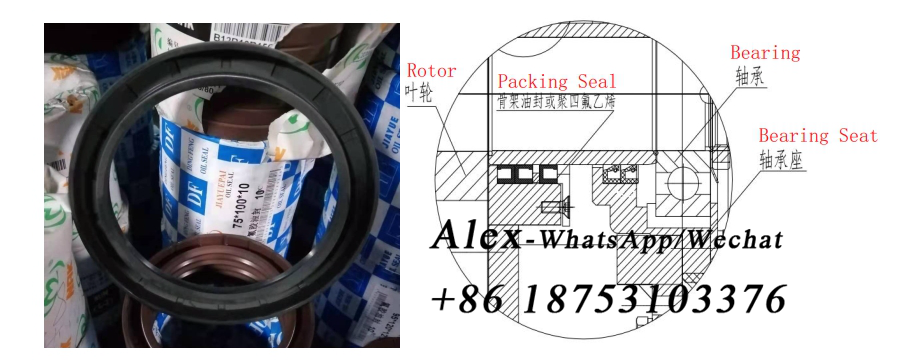
Common packing materials include:
- Gland packing.
- Pre-formed PTFE packing.
- Skeleton oil seal group packing.
Since this seal type involves contact, wear may occur between the shaft and the oil seal lip or PTFE packing. Despite this, its simplicity, low cost, and good sealing performance make it popular in industries such as fertilizer manufacturing.
1.3 Expansion Ring Seal
This seal uses several slotted elastic rings placed in the sealing groove. The rings’ elasticity ensures tight contact with the housing. The gas can only leak downstream through the gaps between the expansion ring and the annular groove.
When operating, high-pressure gas entering the gap strengthens the seal between the expansion ring and the inner bore of the sealing seat. Minimal leakage occurs due to the tiny slit size, further improved with additional pressure-sealing devices.
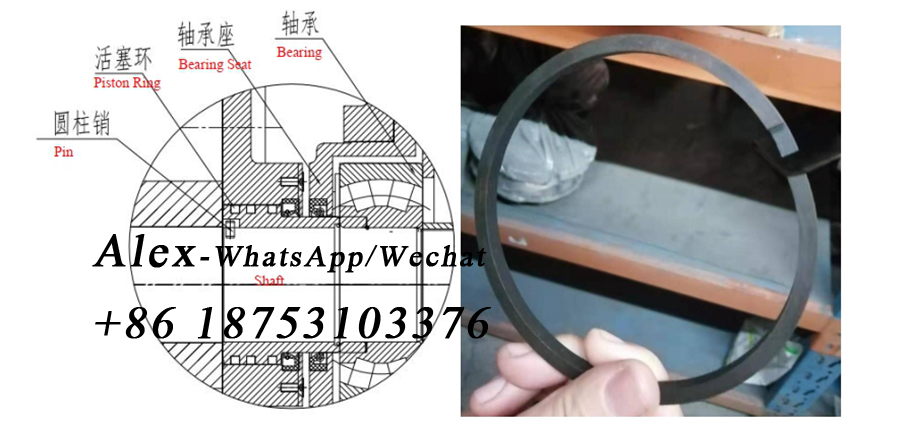
Advantages:
- Good sealing performance due to contact design.
Disadvantages:
- Requires grease lubrication, although special materials allow for lubrication-free use.
The wall plate shaft seal can adopt any of these three forms. Open wall plate structures prevent the conveyed gas from entering the oil tank but may allow leakage into the atmosphere. Conversely, closed structures may result in gas entering the oil tank, and during vacuum pumping, oil might leak into the casing.
2. Mechanical Seal
Also known as end-face seals, mechanical seals limit fluid leakage along the rotating shaft. These seals consist of a stationary ring, a rotating ring, elastic or magnetic elements, rotating ring transmission components, and auxiliary sealing rings.
Working Principle: The sealing function is achieved through the relative rotation of the stationary and rotating rings and the auxiliary sealing elements.
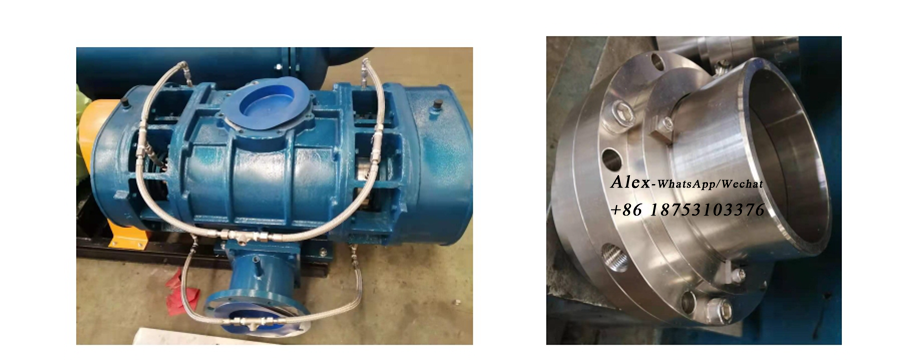
Advantages:
- Reliable operation with minimal leakage.
- Long service life with self-compensating wear on the sealing surfaces.
- Low power consumption and no shaft wear.
Mechanical seals are widely used in industries such as machinery, petroleum, and chemicals. However, they are complex, require high precision, are costly, and can be challenging to maintain.
Roots blowers use two types of mechanical seals: K-type and N-type.
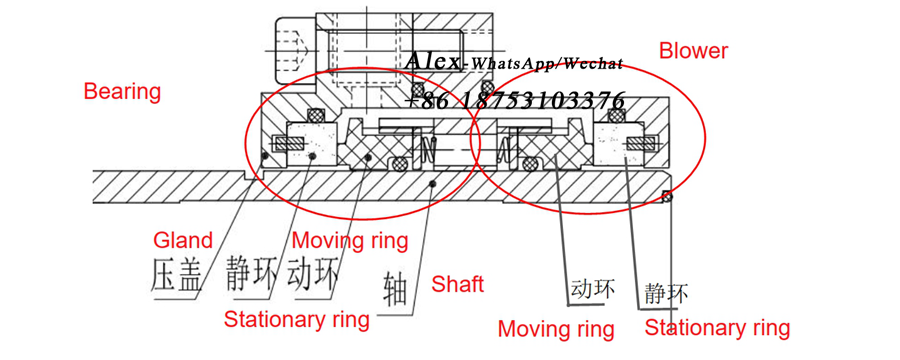
K-Type Mechanical Seal
In this configuration, the drive shaft extension is sealed with a mechanical seal, while the wall plate shaft uses labyrinth or packing seals. This configuration is suitable for inert gases such as nitrogen, where the gas does not degrade the oil.
N-Type Mechanical Seal
This configuration involves four mechanical seals at the wall plate shaft, providing minimal gas leakage and approximating zero leakage. It is particularly effective for gases that degrade lubricating oil.
Conclusion-Roots Blower Sealing Forms
Given the variety of roots blower sealing forms, selecting the appropriate sealing type based on the characteristics of the conveyed medium is crucial. For air transport, labyrinth seals are suitable. Packing seals are ideal for less clean media like coal gas. For flammable, explosive, and toxic gases in industries such as petroleum and chemicals, mechanical seals are recommended. K-type seals are appropriate for inert gases, while N-type seals are necessary for corrosive gases.